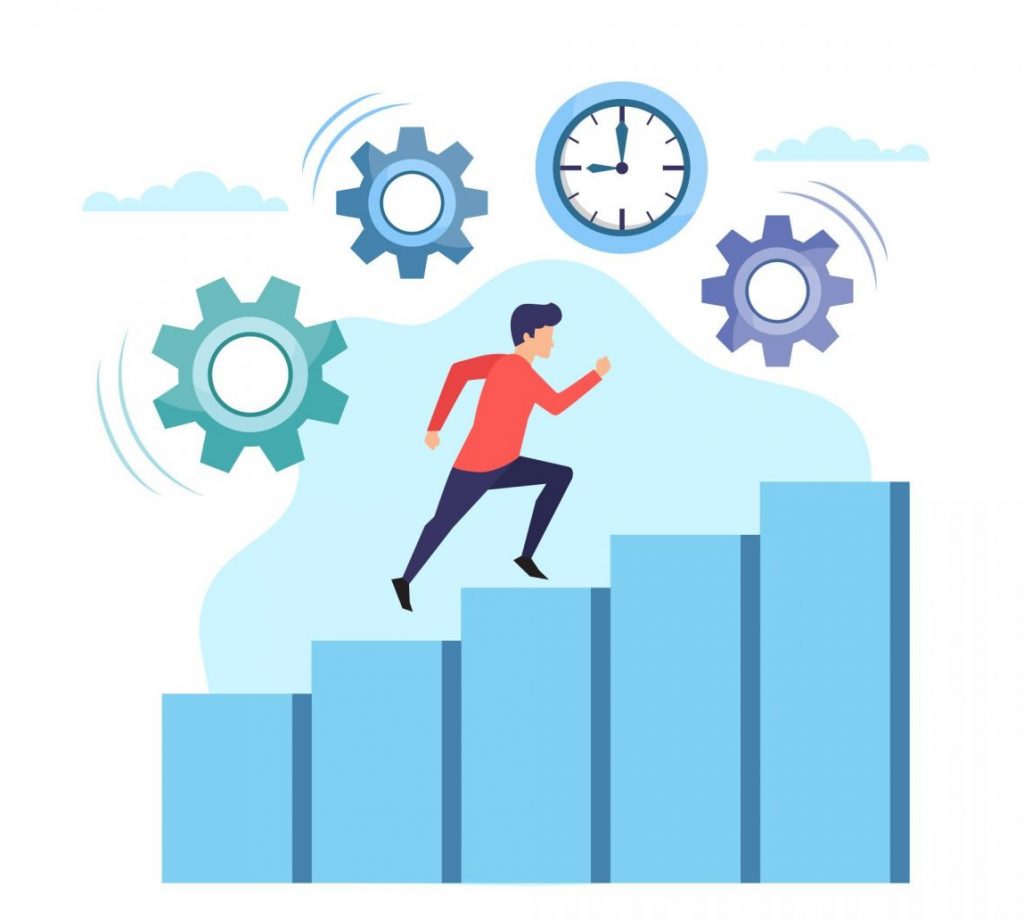
Lean construction methodologies will improve construction performance with respect to cost, time, and quality. The term “kaizen” was introduced in America in 1986 with the publication of Masaaki Imai’s book, Kaizen: The Key to Japan’s Competitive Success, which became widely used and accepted among industrial managers and companies that make use of this philosophy (Recht & Wilderom, 1998; Martin & Osterling, 2007; Al-Smadi, 2009; Suárez-Barraza et al., 2011, 2012). Imai (2012) explains that in the Japanese language, kaizen means “continuous improvement” and that, in practice, it seeks to involve all the participants of the process that is being analyzed at a relatively low cost for the company.
Kaizen, Kaikaku, Kakushin
As discussed above, Kaizen refers to incremental improvements in the workplace. The most popular methodology for Kaizen is Quality circles or Small Group Activities.
Kaikaku – Japanese word for ‘radical change’ refers to a larger revolutionary change. It could be an enterprise wide-ranging project, that brings in large savings or improvement to the process or product.
Kakushin refers to an ‘innovative or a transformative’ change which will result in a complete departure from the current situation. It could be a total newly conceptualized product or a market-disrupting process/service.
Kaizen is the base. Its the building block on top of which Kaikaku and Kakushin can be done. The objective is to remove any non-value adding work by doing kaizen and then see what needs to be done. This is accomplished by eliminating waste.
Muda is a Japanese word meaning “futility; uselessness; wastefulness”, and is a key concept in lean process thinking. There are 7 types of Muda commonly identified in lean manufacturing:
- Overproduction
- Waiting
- Transportation
- Over-processing
- Movement
- Inventory
- Making Defective Parts
Lean Construction
Lean construction is a philosophy to design production systems to Minimize waste of materials, time, and effort in order to generate the maximum possible amount of value. LEAN is an acronym that stands for Leadership. Eliminate waste. Act Now.
A way to do more & more with less & less – less effort, less equipment, less time & less space – whilst providing customers with exactly what they want. In construction, it means improving cost, time, quality, and safety simultaneously without a trade-off.
Lean construction principles basically involve,
- The elimination of waste, especially within the process, in a strategic and considered manner, and
- By creating a continuous flow
Lean Kaizen is a proven approach to continuously implement much-needed change and get rid of unnecessary waste. Lean or Kaizen in Construction is a production management-based approach to project delivery to maximize value and minimize waste. Lean Construction or Kaizen in construction is all about identifying waste in construction design and building processes, which has been revealed as a big percentage of total project costs. In Construction, we talk about big three – Quality, cost, and schedule.
The construction industry has seen an erosion of efficiency with the limited improvement compared to other industries over the past 50 years. The industry has created silos of various supply chain members, introducing significant waste to the system. Individual designers, craftsmen, managers, and suppliers have been isolated and directed to provide only what they have been told, and little has been asked of them outside the realm of their transactional contract obligation.
In order for improvement to take place, the current state should first be bench-marked. The team Value Stream Maps its current state and defines and collects metrics with respect to time, cost, quality, safety, and morale.
Types of waste in Construction
Waste can take on many forms within the building process. Below are some common examples:
1. Building ahead of demand/time
Essential features of lean construction include a clear set of objectives for the delivery process, aimed at maximizing performance for the customer at the project level, concurrent design, construction, and the application of project control throughout the life cycle of the project from design to delivery. Some techniques are discussed below
- Value Stream Mapping: “VSM” is considered among the most used Lean Construction tools for the identification of the sources of wastes. VSM consists of creating a visual map of the flow of materials and information from suppliers to consumers.
- Just in Time: “Just in Time” is classified between the most developed Lean Construction tools designed to eliminate non-value-added activities and to reduce process variability. Just-In-Time philosophy is based on the concepts that stocks which do not bring added value to the customer (internal or external) should be considered as sources of wastes
- Kanban Board / Card: Supply management using “kanban” cards is a very effective technique to ensure the minimum amount of materials, depending on the real needs of the site construction
Few examples of from Construction sites are: Non-standardized construction processes, design drawings revisions, Multiple delivery/storage schedule, etc
2. People & Process
Lean is a management system that relies on a team-based collaborative problem-solving methodology. The target condition we seek is everybody, every day coming together and asking three simple questions:
How did we do yesterday?
Where was the waste?
How can we do it better today?
When we commit to this, people must change responsibilities and behaviors change as a result. Workers now play an integral role in solving problems. Leaders become coaches building the problem-solving muscle of their teams. Everyone is committed to working as a team to identify and solve problems. Also, we need to research on untapped human potential to effectively improve the process from within.
Few examples of from Construction sites are: Lack of communication, changes in design by client, commercial pressure, schedule, information flows, work flexibility on site
3. Logistics & Transportation
This can be the transportation of equipment, materials, and workers to a job-site before they are needed or it can refer to the transmission of information with no added value.
Few examples of from Construction sites are: Delayed Logistics, Loading & Unloading delays, Union Issues, Vehicle Movement, etc
4. Material Management
Supply logistics plays a strategic role as it operates in the production and supply interface besides having a significant contribution to the total costs of an enterprise. At the same time, the supply logistics is responsible for the interruptions at the workstations, as well as for the loss of productivity. Applying modularity to the product design, the outsourcing of components, and the organization of production and supplies are viewed as an improvement strategy of the order fulfillment process and supply chain structure.
Few examples from Construction sites are: Material waste produced in the site, Bulk Procurement, Obsolete Materials, Material Loss at the site, etc
5. Motion Waste
The motion requires energy and time. Therefore, there is a need for reducing the motion that does not provide value during the production process, which includes moving to bring raw materials to production cells and moving to bring tools.
A motion is considered to be adding value when it is a part of the process and has a direct influence on the product in terms of its value to the customer. As waste refers to processes that do not add value to the organization, motion that does not add value is considered waste. In the lean principle of manufacturing, minimizing motion is aimed at decreasing overburden and enhancing efficiency
Few examples from Construction sites are: Searching for supplies, Procurement Lead time, Wrong deliveries, etc
Workplace organization (5S or CANDO)
5S principles involve improvement to processes generally through good housekeeping and sensible workplace organization. These 5 principles are basically:
Cleanliness
- General tidying up
- Removing from the landscape all items that are not in use, not required by the current
- activity
- This means inventory – only that which is needed for that activity no more than a days
- worth
- Improve, and keep rigorous paperwork
Arranging
- Determine a place for everything to be kept
- Material to be arranged to minimize waste on motions- double handling
- Shadow boards for tools
- Visual Management
Neatness
- Everything in its place and ready to go
- Visual management seeing where everything is
- 5-minute cleanups on the hour
- Plans, schedules, risk assessments, Takt time all displayed
- Responsibilities for neatness assigned
Discipline
- Don’t Do it-stop the line!
- One thing at a time latest start earliest finish
- Establish routines
- Conduct regular audits
Ongoing Improvement
- Maintaining the tempo of everything we do
- Getting to the root cause of the problems
- Stretching to reach the targets
- Learning to see waste and improve our performance
- Challenge what has gone before
Applying Lean thinking has transformed many industries and its implementation in construction has now started to show the potential benefits. The lean approach is the only way that improvements in time, cost, and quality can be made simultaneously without a trade-off. Lean construction focuses on delivering precisely what the client and end-user want.