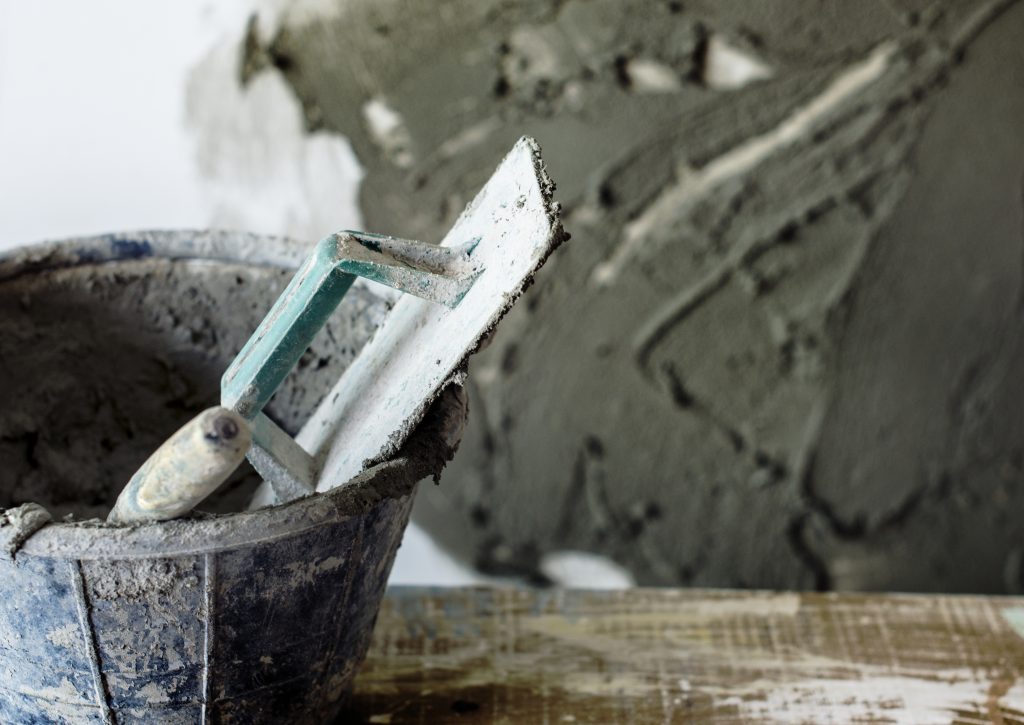
Cement is one of the most consumed products in the construction industry as it plays a vital role in providing strength and durability for the building. Quality of cement you choose for construction will determine the longevity, resistance to adverse weather conditions and other factors that may cause any degradation of your building.
While there are various types of cement, 2 most used for retail construction are OPC (Ordinary Portland Cement) and PPC (Portland Pozzolana Cement). OPC is then further available in various gradations based on compressive strength it will attain on 28 days of setting: Grade 33, Grade 43 and Grade 53.
Types of Cement
This cement is suitable for masonry and other general concrete use during normal environment condition. Generally, usage is low.
Is used mainly for high rise buildings and other general masonry works like plastering, flooring etc.
It attains a compressive strength of 43 MPA (Megapascals) within 28 days of its setting. It is also used in construction of precast items like blocks, tiles etc. For a concrete grade of up to M30, OPC 43 can be used.
Any structure that requires an initial strength is made using OPC 53. It also has faster setting capacity compared to OPC 43.
It’s main use is in RCC and prestressed concrete of high grades.
Portland Pozzolana Cement (PPC)
Is one of the most used cement for all the purpose of both structural works and non-structural works.
It is confidently employed in construction of hydraulic structures, marine works, mass concreting such as dams, dykes, retaining walls foundations and sewage pipes etc.
It is also suitable for use in common applications such as masonry mortars and plastering. PPC cement is usually more economical than OPC cement.
8 quality checks to ensure you are using the right Cement:
- Date of Packing: Check for the date of packing on the cement bag. The Cement strength reduces by time.
- Color of cement: The cement in a batch should contain uniform color. The difference in color indicates excess lime or clay and degree of burning.
- Rubbing of Cement: Take a pinch of cement between fingers and rub it. The cement should feel as fine and smooth while rubbing.
- Hand Insertion: Thrust your hand into the cement bag and it should give a cool feeling, It indicates that no hydration reaction is taking place in the bag.
- Float Test: When we throw the cement in a bucket full of water, the cement should sink and not floated on the water.
- Smell Test: Take a pinch of cement and smell it, It should not have any earthy smell.
- Presence of Lumps: In a bag of cement, when we open it, there should not be any lumps which ensures no setting has taken place.
- Strength Test: To do the test:
- -Prepare a Block of cement 25 mm x 25 mm and 200 mm long,
- Then immerse it in water for 7 days,
- Place it on support, 15000 mm apart and loaded with a weight of 340N.
Result: The block should not show any sign of failure.
Share your thoughts below:
1.initial setting time and final setting time.
2.soundness test.
3.consistency of water cement ratio.
Theses are most important tests.
1. How long the cement will be good from the date of packing?
2. Which color indicates “ excess lime or clay and degree of burning.”
3. If I put my hand in cement bag to check cool feeling and if there hydration process going on, “does it hurt?” It’s a chemical reaction !!!
Cement should be used within 3 months from the date of manufacturing , If we kept more than 3 months the cement need to be re tested.
The ideal colour of cement is greenish Grey. The light grey colour indicates that cement may be an older one or excess lime or clay and degree of burning.